Un client choisit la couleur de son casque de vélo, ajoute une puce NFC pour le suivi post-vente, puis valide sa commande. Dans l’atelier, une ligne flexible réserve instantanément le bon moule, le robot de peinture charge la teinte « RAL 3020 » et la logistique déclenche l’approvisionnement de la puce NFC en juste-à-temps. La promesse : livraison en sept jours, produit unique et coûts maîtrisés.
Cette « séquence idéale » s’appuie sur un socle numérique déjà très présent : selon le Ministère de l’Économie, 64 % des entreprises manufacturières françaises exploitent désormais l’automatisation et la maintenance prédictive pour optimiser leurs processus. Or, dans la réalité, il subsiste souvent quelques points manuels, même chez les industriels les plus avancés. En effet, connecter ces briques au portail client et synchroniser la production à la demande reste le défi majeur.
De la production de masse à la personnalisation à la demande
Pendant des décennies, l’équation industrielle était simple : économies d’échelle, stocks tampons, catalogue figé.
Aujourd’hui, la volatilité des marchés et la pression écologique ont changé la donne.
Le client comme planificateur
L’utilisateur final configure désormais le produit avant même qu’il n’existe. Chaque clic devient une exigence qu’il faut traduire en nomenclature, capacité machine et ordonnancement.
Petites séries, gros enjeux
Dans l’électronique ou l’agroalimentaire premium, les lots de 500 pièces sont devenus la norme. Le risque ? Une rupture de stock sur une couleur ou un packaging spécifique ruine la promesse de délai et fait exploser les coûts de reprise.
Un accélérateur : l’impression 3D
En quelques années, l’impression 3D s’est imposée comme un (le ?) moyen pour produire des pièces uniques ou en très petites séries sans coût de moule ni délai de fabrication prolongé. Cela transforme la manière de prototyper, en passant de plusieurs semaines à quelques heures entre l’idée et la pièce tangible. Elle devient aussi un outil de personnalisation de masse : chaque client peut obtenir un produit modifié à la demande, sans rupture dans le flux industriel. L’impression 3D réconcilie ainsi agilité et industrialisation, tout en réduisant les stocks et les transports.
Petites séries : un défi de synchronisation de bout en bout
Produire à la demande, c’est donc orchestrer un ballet millimétré entre commandes, ingénierie et shop-floor.
La personnalisation introduit une variabilité extrême : chaque commande devient quasiment un prototype, mais doit circuler dans des lignes industrielles qui, historiquement, visaient la répétition. D’où un besoin accru de pilotage temps réel pour préserver coûts et délais.
Les 3 maillons sous tension :
- Planification dynamique : adapter la charge atelier en temps réel quand un client modifie sa commande à J-1.
- Disponibilité matière : sécuriser un circuit d’approvisionnement souvent multiplié par dix du fait de la personnalisation.
- Qualité sans retouche : garantir qu’une variante ne dégrade pas le taux de rebuts ni les certifications.
Lorsque l’un de ces maillons patine, le lead-time s’allonge et l’avantage concurrentiel disparaît. Seule la maîtrise fine des processus, visible de bout en bout, peut absorber ce niveau de variabilité.
« Ces trois écueils se manifestent à chaque nouvelle variante et font exploser le lead-time si la chaîne n’est pas pilotée au signal client. »
Le BPM, passerelle directe entre client et atelier
Le Business Process Management fournit ce chaînon manquant : un langage commun (BPMN 2.0) et un moteur d’exécution qui tisse un flux continu entre front-office et machines.
Quand le client déclenche le flux
Une API de configuration produit ou un EDI partenaire déclenche un process « commande personnalisée ». Le BPM :
- vérifie la faisabilité technique (appel au PLM) ;
- calcule le prix dynamique ;
- réserve la capacité machine dans le MES (logiciel de pilotage de la production) ;
- propose un créneau de livraison en s’appuyant sur le TMS (système de gestion du transport).
À chaque jalon, il publie un événement que le client visualise dans son portail. Résultat : transparence et engagement sans surcoût humain.
Automatisé, mais contrôlé
Certaines étapes restent évidemment manuelles (validation design, contrôle qualité « œil humain »), mais elles sont intégrées comme des tâches adressables, horodatées, traçables.
En cas de non-conformité, le BPM déclenche un circuit d’escalade et réoriente l’ordre de fabrication.
Un Système d’Information hyperconnecté pour une exécution sans couture
Bien entendu, orchestrer ne suffit pas, encore faut-il que chaque application parle la même langue.
ESB et API pour recoller les briques
Un bus applicatif gère la médiation : l’ERP envoie un ID commande, le MES travaille avec un ID ordre de travail, le WMS parle codes barres. La couche ESB transforme, enrichit, distribue en temps réel. Un portail d’API ouvre ensuite ces services aux partenaires ou aux clients.
Process Mining, l’électrocardiogramme de l’usine
Une fois le flux automatisé, l’enjeu devient l’amélioration continue. Grâce au Process Mining, le déroulé exact des ordres de fabrication est reconstruit à partir des logs machines. Il révèle les goulets, propose de nouvelles séquences et alimente la mise à jour du modèle BPMN.
Gouvernance de la donnée
Enfin, qui dit petite série, dit explosion des variantes. Un référentiel de données consolide nomenclatures, versions produit, profils clients. Sans lui, impossible de livrer la bonne déclinaison ni de rapprocher coûts et marge réelle.
Automatiser sans aveuglement, pour une personnalisation industrielle sous contrôle
Chez Blueway, nous considérons que produire à la demande n’est viable que si chaque événement reste traçable et chaque déviation, corrigeable.
Notre plateforme Phoenix réunit les usages BPM, MDM, ESB et API Management. Grâce à cette approche exhaustive des flux d’informations, elle intègre également la démarche de Process Mining.
Résultat : des flux hyper-automatisés, mais toujours auditables, gouvernables, évolutifs, les trois conditions pour faire de la petite série personnalisée un atout compétitif durable.
Article mis à jour le 21/05/2025
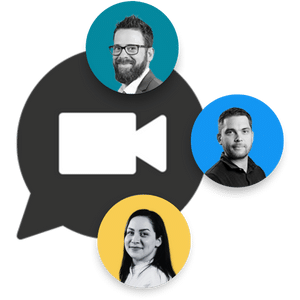
Échangez sur le BPM avec un expert Blueway !